Kupfer IMS PCB | Leiterplatte | Platine
Kupfer IMS PCB Leiterplatten (Platinen)
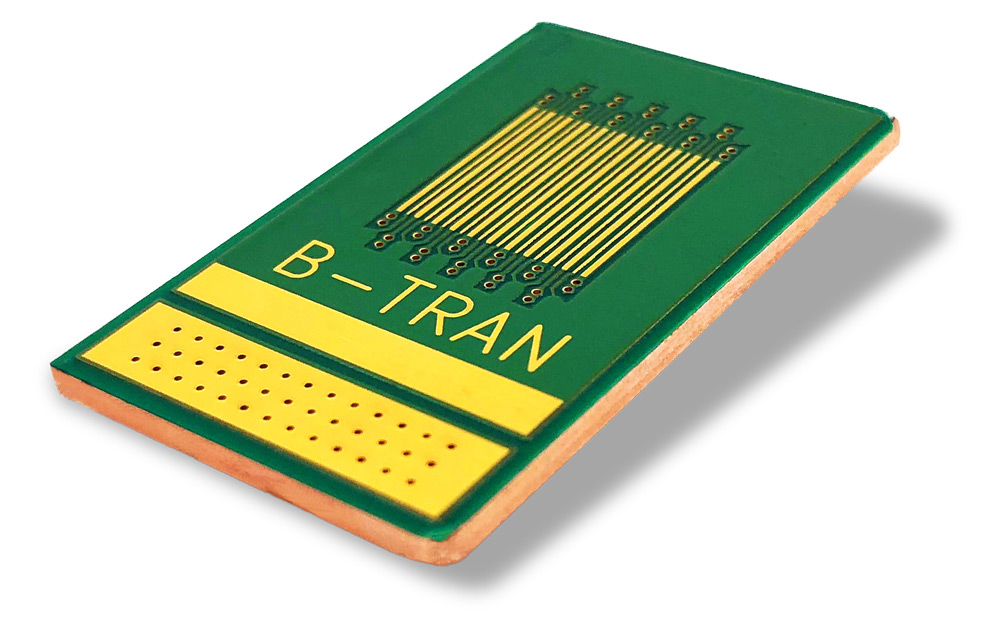
Das Alu “brennt” schon? Keine Ahnung, wohin mit der Wärme? Oft bleibt dann nur noch das Upgrade auf Kupfer-IMS-Leiterplatten.
Hier eröffnet sich ein Spektrum an vielen neuen Möglichkeiten: höherer Wärmeleitwert, elektrische Kontaktierung vom Leiterbild mit dem Kupferträger und Lötbarkeit des Basisträgers können wichtige Vorteile darstellen.
Durch den vielfach erprobten, zuverlässigen Verbund zwischen Kupfer allgemein und Isolationsschichten (Prepregs) in der Leiterplattenfertigung, lassen sich hier auch sehr stabile, individuelle Sonderaufbauten realisieren, wo das IMS-Kupfer flexibel positioniert oder in der Dicke gewählt werden kann.
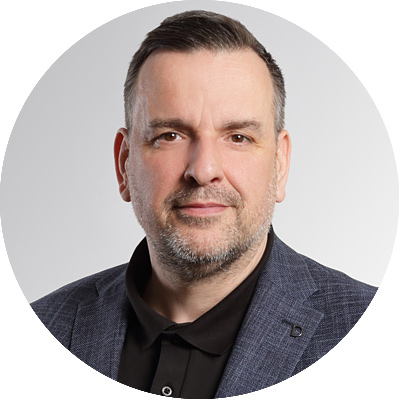
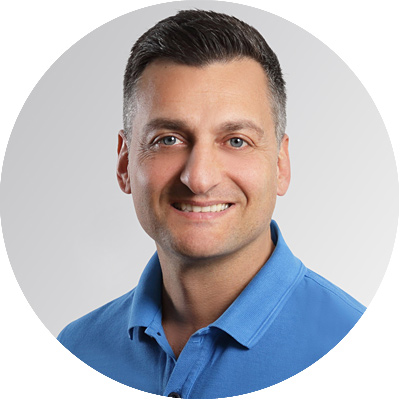
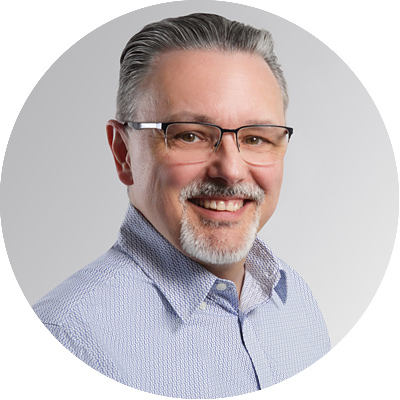
Optionen |
---|
Materialeigenschaften | 1,0 - 3,0 W/mK, 38 - 100µm Isolation |
Materialhersteller | TCLAD (Bergquist), Ventec und Hausmarken |
Materialdicken | 0,8 / 1,0 / 1,6 / 2,0 mm |
Maximale Leiterplattengröße | 428 x 568 mm², weitere Übergrößen auf Anfrage |
Kupferdicken | 35µm / 70µm |
Lagenzahl | 1 bis 2 Lagen |
Oberflächen | ENIG (chemisch Gold) |
Mechanische Bearbeitung | Fräsen, Ritzen, Sprungritzen, Senkbohrungen |
Bohroptionen | Isolierte Bohrungen, durchkontaktierte Sacklöcher |
Metallisierungen | in den Träger möglich |
Lötstopp | Lack, Hochreflektionslack, Abdeckfolie (Coverlay) Coverlay-Farben: gelb, weiß, schwarz Lackfarben: grün, gelb, weiß, schwarz, Sonderfarben, Matt-Lacke |
Sonderlacke | Bestückungsdruck, Abziehlack, Karbondruck |
Sondertechnologien | Mehrlagen Kupfer-IMS als Träger- und Kern-Variante, Kontaktierung der Kupferfläche mit Kupferträger (z.B. durch Sacklöcher) |
Qualitätsmanagement & Zertifizierungen | ISO 9001, ISO 14001, UL, IPC2/IPC3, IATF 16949, EMPB, VDA2, PPAP, Schliffe, Vermessungen, Konformitätserklärungen, Datenblätter, ESD-Verpackung uvm. |
Logistik | Rahmenaufträge, Konsignationslager, Abruflager, See-Luft-Split-Aufträge |
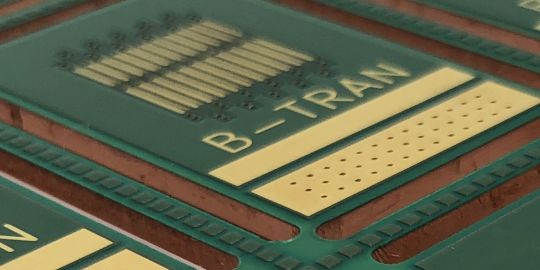
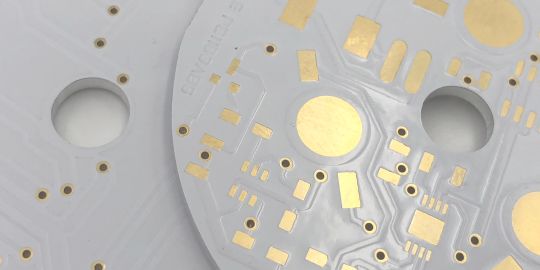
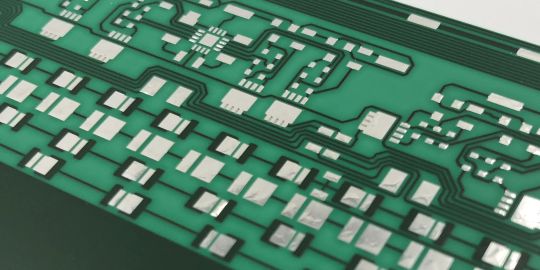
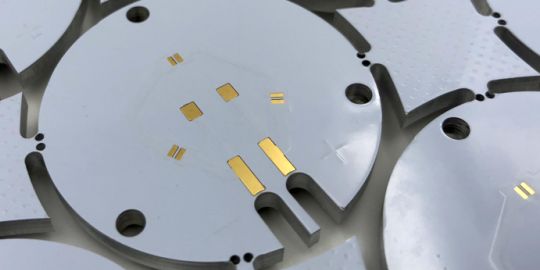
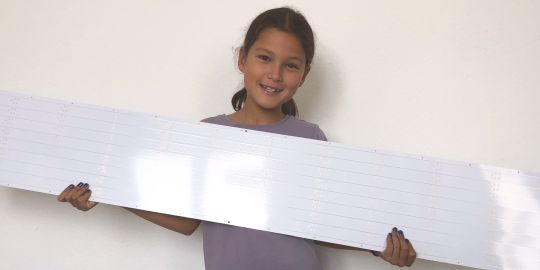
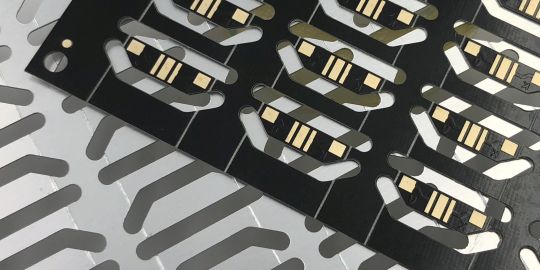
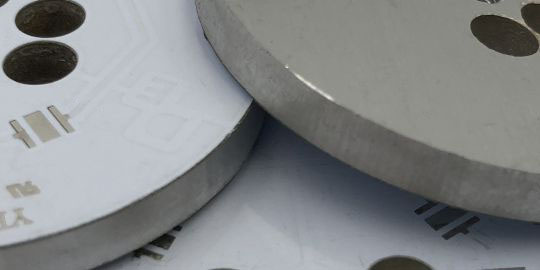
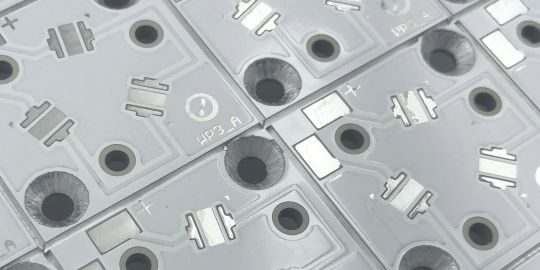
Definition: Kupfer-IMS PCB
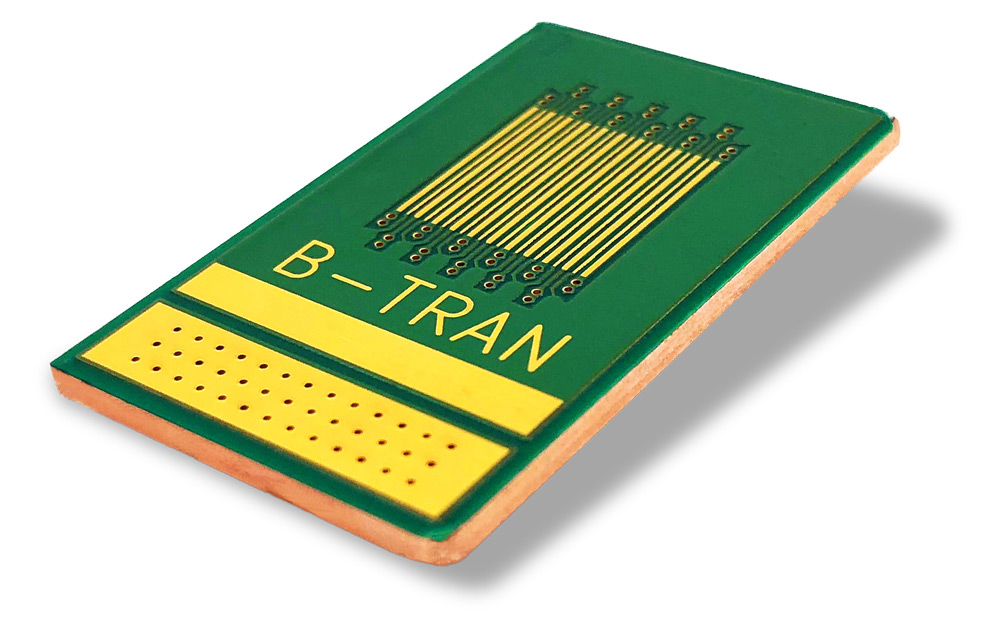
IMS steht für “Insulated Metal Substrate”. PCB steht für "Printed Circuit Board". Zu Deutsch: Leiterplatte mit isoliertem Metallsubstrat. Dabei wird die Stromleitende Kupferschicht der Leiterplatte von dem dickeren Kupfer des Metallträgers isoliert. Die Isolationsschichten sind üblicherweise 50 bis 100µm dick. Die Gesamtdicke einer Kupfer-IMS-Leiterplatte beträgt meist 1,0mm oder 1,6mm, abweichende Dicken sind erhältlich. Die Kupferschicht für die Elektronik ist 35µm oder 70µm dick, wobei dickere Kupferschichten teilweise möglich sind.
Vorteile von IMS-Leiterplatten & Platinen aus Kupfer
Kupfer-IMS-Platinen haben Vorteile, wenn es um das Wärmemanagement geht:
- Sehr hoher Wärmeleitwert von Kupfer (ca. 380W/mK)
- Sehr gute Kontaktierungsmöglichkeit (z.B. Heat-Sink-Sacklöcher in den Metallträger
- Sehr guter Haftverbund bei Multilayern
- Sehr gute Löteigenschaften (Träger kann mit Lot kontaktiert werden)
Den Vorteilen stehen gewisse Nachteile entgegen. so sind Kupfer-IMS-Leiterplatten zum einen sehr schwer. Ferner sind sie deutlich teurer als FR4 oder Aluminium-IMS-Leiterplatten (ca. Faktor 5-10).
Anwendungsmöglichkeiten von Kupfer-IMS PCB
Durch die deutlich höheren Kosten von Kupfer-IMS-Leiterplatten im Vergleich zu Aluminium-IMS-Platinen, kommen diese eigentlich nur in Frage, wenn entweder das eingesetzte Aluminium von den Wärmeleiteigenschaften nicht ausreicht, oder es technisch erforderlich ist, den Kupferträger elektrisch zu kontaktieren. Während diese mit Aluminium nicht möglich ist, kann man zum Beispiel Sacklochbohrungen in den Kupferträger bohren und diese dann durchkontaktieren und somit thermisch und elektrisch anbinden.
Arten von IMS Leiterplatten
Gänge IMS-Leiterplatten haben meist Aluminium als Metallträger. Kupfer ist vergleichsweise selten dagegen. In extrem seltenen Fällen werden auch ganz andere Metalle verarbeitet, wie Edelstahl.
Kupfer PCB Eigenschaften
Aluminium PCB Eigenschaften
Die Herstellung unserer Kupferplatinen & -leiterplatten
1-lagige Kupferplatinen gleichen dem Herstellungsprozess von normalen FR4-Leiterplatten, es sei denn, es werden Bauteilbohrungen benötigt. Solche Bohrungen müssen stets vorab größer vorgebohrt, mit Paste isoliert und später in der erforderlichen Größe in die ausgehärtete Isolationspaste nachgebohrt werden, damit es keine Kurzschlüsse zum Kupferträger gibt. Wenn 2-lagige Kupfer-IM-Platinen mit dem Kupfer als Kern (mittig) hergestellt werden, wird zunächst der reine Kupferkern vorgebohrt, die Löcher mit Paste isoliert und dann mit isolierenden Prepregs die Kupferschichten auflaminiert. Anschließend gleicht der Herstellungsprozess dem einer normalen 2-lagigen Leiterplatte.
Günstige Kupfer IMS Leiterplatten direkt vom Hersteller online kaufen
Kalkulieren und bestellen Sie Kupfer-IMS-Platinen einfach und komfortabel zu fairen Preisen in unserer Onlinekalkulation oder fragen Sie uns per E-Mail an und wir senden Ihnen ein attraktives Angebot zu. Gerne beraten wir Sie auch ausführlich zu diesem Thema.
Thermal-Blind-Vias sind auf Kupfer-IMS-Platinen ebenfalls möglich.
Kupferkern-Heat-Sink-Leiterplatte
Bei diesem Beispielprojekt wurden auf einer Gesamtdicke von 4,2mm zwei 1,8mm Vollkupferflächen eingebettet und mit zusätzlichen Heat-Sink-Sacklöchern angebunden. Wie bei einem normalen 4-Lagen Multilayer verlaufen zwischen den Kernen zwei Signalinnenlagen. Es handelt sich um eine Kombination aus komplexer Schaltung mit integriertem Hochleistungswärmemanagement.
LED- und Hochleistungselektronik stellen große Herausforderungen an das Wärmemanagement von Leiterplatten dar. Während Aluminium-Platinen heute gängiger Standard sind, wurde hier für extreme Anforderungen ein Kupferkern-Heat-Sink-Multilayer hergestellt. Die massiven Kupferkerne wurden mit Heat-Sink- Sacklöchern an die Außenlagen angebunden, um eine optimale Wärmeableitung zu gewährleisten.
Unbehelligt vom Wärmemanagement befindet sich ein komplexer 4-Lagen Multilayer in diesem Aufbau. Die benötigten Anbindungen an Außenlagen wurden zuerst aus den Kupferkernen freigestellt, dann Isoliert, gebohrt und durchkontaktiert. Dank digitaler Z-Achsensteuerung für Sacklöcher können die Heat-Sinks sehr präzise gesetzt werden und die Packungsdichte des Multilayers wird kaum beeinträchtigt.
Die Innenlagen zur reinen Signalansteuerung wurde mit einem Standard 18µm Kupfer erstellt, während die Außenlagen mit 50µm hergestellt wurden, um den hohen Strömen dort gerecht zu werden. Das Hülsenkupfer der Durchkontaktierungen betrug trotz der enormen Lochtiefe von 4,2mm auch in der Mitte noch über 20µm.
Zum Verpressen wurde spezielles wärmeleitendes Prepreg mit einem Wärmeleitwert von 1,3W/mK verwendet. Dieses unterstützt auch auf Flächen ohne Heat-Sink-Sacklöcher die Wärmeabfuhr zum Kupfer-Massivkern hin. Übliche Wärmeleitwerte von Standard-Prepregs liegen bei nur 0,3…0,4W/mK.
Eigenschaft | Werte, Erläuterung |
---|---|
Materialart | FR4, Tg 150°C mit Kupfer |
maximale Dicke | bis 4,8mm |
mögliche Kupferkerndicken | 1,0mm / 1,5mm / 1,8mm / 2,0mm |
Kupferdicken (Signallagen) | 35µm, 55µm, 70µm, 105µm, Innenlagen auch 18µm |
maximale Lagenzahl | abhängig von Kupferkerndicken bis 8 Lagen |
Wärmeleitwert Prepreg | 1,3 W/mk |
Wärmeleitwert Kupfer | ca. 380W/mK |
Lagenanordnung | bis zu drei Kupferkerne, auch asymmetrische Anordnung |
Aspekt-Ratio Thermal-Sacklöcher | 1:1 |
IMS-PCB steht für "Insulated Metal Substrate Printed Circuit Board" und ist daher eine Leiterplatte mit einem Metallsubstrat (Kupfer oder Aluminium), welches von der elektronischen Schaltung isoliert wird. IMS PCBs werden oft für Anwendungen verwendet, bei denen effiziente Wärmeableitung erforderlich ist, da das Metallsubstrat Wärme besser leitet als herkömmliche Substrate wie FR4. Dies macht IMS PCBs besonders geeignet für Leistungselektronik, LED-Beleuchtung, Automotive-Anwendungen und andere Bereiche, in denen Wärmemanagement eine wichtige Rolle spielt. Die Wahl zwischen Aluminium-IMS und Kupfer-IMS hängt von den spezifischen Anforderungen der Anwendung ab, da beide Materialien unterschiedliche Wärmeleitfähigkeiten und Kosten aufweisen.
Herkömmliche Leiterplatten verwenden ein sogenanntes FR4 als Basismaterial, was aus einem nicht-leitenden Epoxidharz-Glasfasergemisch besteht. Bohrungen können so zum Beispiel durch dieses Basismaterial gefertigt und direkt durchkontaktiert werden. Bei IMS-Leiterplatten wird hingegen ein Metallsubstrat (Aluminium oder Kupfer) als Basismaterial verwendet. Bauteilbohrungen dürfen daher nicht einfach in das Material gebohrt werden, sondern müssen mit einer Paste isoliert werden. Als Eigenschaft von IMS-Leiterplatten wird häufig der Wärmeleitwert in W/mK (Watt pro Meter x Kelvin) genannt. Dieser bezieht sich nicht auf den Wärmeleitwert des Metallsubstrats, sondern auf die Isolationsschicht zur Kupferschicht, welche die elektrische Funktion herstellt.
Ein Vorteil von Kupfer-IMS-Leiterplatten gegenüber Aluminium-IMS-Leiterplatten liegt zum einen in dem höheren Wärmeleitwert (Kupfer ~380W/mK versus Aluminium ~240W/mK). Ein weiterer Vorteil ist die Möglichkeit, das Trägerkupfer mit Sacklöchern elektrisch zu kontaktieren. Auch kann man den Kupferträger zum Beispiel mit ENIG vergolden. Beides ist mit Aluminium nicht möglich. Nachteile von Kupfer-IMS-Leiterplatten sind hingegen das deutlich höhere Gewicht (Kupfer 9g/cm³ versus Aluminium 2,8g/cm³) und der höhere Preis (Faktor 6 bis 10).
Vorteile von Kupfer-IMS-Platinen:
- Kupfer als Wärmeleiter
- Diverse Gesamtdicken von 0,8 bis 2,0 mm wählbar
- Kupferschichten von 35µm oder 70µm
- Isolationsschicht 38 bis 100µm
- Wärmeleitfähigkeit ~380W/mK
- gut chemisch kontaktierbar (chemische Vergoldung des Trägers möglich)
- Kupferträger ebenfalls gut lötbar
Nachteile von Kupfer-IMS-Platinen:
- Sehr schweres Material (spezifisches Gewicht 9g/cm²)
- Sehr teures Material (Faktor 6 bis 10 zu Alu-IMS)
IMS-Leiterplatten helfen primär dadurch, dass sie Hitze von elektronischen Bauteilen ableiten, sie also den thermischen Stress reduzieren. Durch diese geringere Hitze haben Bauteile allgemein eine teils deutlich längere Lebenszeit, was die Ausfallsicherheit und Zuverlässigkeit der Elektronik erhöht. Der Vorteil von Metallen wie Aluminium oder Kupfer ist zudem, dass die sehr gute Wärmleitfähigkeit dafür sorgt, die punktuelle Hitze (“hot spots”) von hitzeemittierenden Bauteilen direkt in den Träger zu verteilen und abzuleiten. Dem Effekt der Wärmableitung in den Metallträger der Leiterplatte können bei Bedarf weitere Kühlungsmethoden hinzugefügt werden. Entweder werden weitere passive Kühlkörper auf den Metallträger montiert und/oder es erfolgt eine aktive Kühlung des Trägers mittels Lüftern oder sogar Wasserkühlung oder anderen Flüssigkeiten.
IMS-Leiterplatten sollte man dann in Erwägung ziehen, wenn es zu großer Hitzeentwicklung durch bestimmte Bauteile (z.B. high Power-LEDs) kommt. Diese Hitze kann sehr schädlich für die Lebensdauer dieser Bauteile sein und IMS-Platinen helfen dabei, diese Hitze effizient von Hot-Spots abzuleiten. Voraussetzung für die Verwendung von IMS-Leiterplatten ist jedoch meist ein relativ einfaches, möglichst einlagiges Design/Layout, denn mehrlagige IMS-Leiterplatten werden schnell sehr teuer.
Die anschaulichste Testmethode zur Überprüfung der Hitzeverteilung in Elektronikbaugruppen ist mit Wärmebildkameras möglich. Diese sind jedoch teuer und nicht immer verfügbar. Wenn man keine Wärmebildkamera hat, kann man mit Thermometern und aufgeklebten Temperatursensoren messen, oder man verwendet Laserthermometer, um die Hitzeverteilung nachzuvollziehen. Beides ist deutlich ungenauer als Wärmebilder, aber eine günstige Alternative, um sich einen allgemeinen Eindruck vom Kühleffekt der IMS-Leiterplatte zu machen.
Um die Hitzeentwicklung von hohen Strömen auf Leiterplatten zu berechnen, bietet Leiton ein einfaches Online-Tool an. Hier kann aus den Parametern “Leiterbahnbreite”, “Kupferdicke”, “Höhe des Stroms” die Temperatursteigerung errechnet werden. Andersherum kann auch die maximal gewünschte Temperatursteigerung vorgegeben werden und das Tool errechnet auf Basis des Stromes die entsprechend notwendige Leiterbahnbreite. Das Ergebnis kann als PDF-Dokument mit Grafik heruntergeladen werden.
IMS-Leiterplatten mit Aluminium als Träger sind sehr weit verbreitet. Es gibt daher zahlreiche Anbieter, die auch kostengünstige IMS-Platinen anbieten. Zu beachten ist hierbei allerdings, welches Basismaterial verwendet wird. Günstige Anbieter verwenden oft Material mit einem sehr geringen Wärmeleitwert der Isolationsschicht (Prepreg) von nur 1,0W/mK. Leiton bietet in seiner günstigen Aluminium-IMS-Onlinekalkulation Prepregs ab 1,5Wm/K diverse Wärmeleitwerte bis hin zu 12,0W/mK high-Performance-Prepreg.
Zudem hat Leiton auch Kupfer-IMS-Leiterplatten in der Onlinekalkulation. Allerdings sind Kupfer-IMS-PCB deutlich teurer als Aluminium.
Auch bei IMS-Leiterplatten ist es wichtig, die Strombelastbarkeit der Leiterbahnen nicht aus den Augen zu verlieren. Leiton bietet hierzu ein kostenloses Tool zur Berechnung der Leiterbahnerwärmung. Auch wenn IMS-Leiterplatten prinzipiell besser die Hitze ableiten, so ist die Erwärmung in den Leiterbahnen maßgeblich für die zu wählende Kupferdicke (35µm, 70µm oder sogar 105µm). Neben Gesamtdicke, welche sich aus der Einbausituation der Elektronik ergibt, ist bei der Wahl der Isolationsschicht (Prepreg) zwischen Metallsubstrat und Leiterbahnen abzuwägen, ob eine sehr dünne Schicht mit guter Wärmedurchleitung auch einem eventuellen Spannungsdurchschlag standhält. Gerne beraten wir Sie hierzu!
Der erste Schritt zur Reduzierung kritischer Hitze auf Leiterplatten ist die Erhöhung des Kupferdurchmessers der stromleitenden Bahnen. Wenn das Layout Platz hergibt, sollten die Leiterbahnen möglichst breit angelegt werden und überall Kupfermasseflächen eingebaut werden. Wenn das nicht reicht, kann die Kupferschicht erhöht werden. Oft reduziert sich die Wärmeentwicklung der elektrischen Schaltung auf ein normales Maß, wenn man von den Standard 35µm auf 70µm oder 105µm erhöht. Weitere Möglichkeiten bieten sogenannte Heat-Sink-Bohrungen oder “Wärmefallen”. Hierbei werden zusätzliche durchkontaktierte Bohrungen in kritische Bereiche eingefügt, die dann Hitze über ihre Kupferwand auf eine andere, meist gegenüberliegende Außenlage, ableiten.
Leiton bietet ein praktisches Online-Tool zur Berechnung der Hitzeentwicklung von Leiterbahnen in Abhängigkeit zum Strom. Benötigt werden Angaben zu “Leiterbahnbreite”, “Kupferdicke” und “Höhe des Stroms”, so dass die Erwärmung errechnet wird. Wichtig ist hierbei, dass die errechnete Wärme zuzüglich zur Umgebungstemperatur zu verstehen ist. Es kann auch rückwärts gerechnet werden, indem man die maximal gewünschte zusätzliche Erwärmung angibt und das Tool eine dafür notwendige minimale Leiterbahnbreite ausrechnet. Das Ergebnis kann als PDF-Dokument mit Grafik heruntergeladen werden.
Wärmefallen im Sinner der reinen Leiterplatten sind durchkontaktierte Bohrungen, deren Zweck nicht das leiten eines elektrischen Stroms, sondern das Ableiten von Hitze ist. Voraussetzung dazu ist meist, dass eine Leiterplatte mindestens 2 Lagen hat, da bei 1-lagigen Leiterplatten kein Durchkontaktierungsprozess stattfindet. Mehrlagige IMS-Leiterplatten haben deutlich höhere Kosten im Bezug. Alu-IMS-PCB haben bei gebohrten Wärmefallen den Nachteil, dass diese zunächst vom Metallsubstrat isoliert werden müssen, da DK-Kupfer nicht am Alu hält. Eine solche Isolierungsbohrung reduziert wiederum den gesamten Anteil am Aluminium in der PCB, bis hin zu dem Fall, dass die Isolationsbohrungen so weit überlappen, dass gesamte Bereiche aus dem Metallsubstrat kein Alu mehr enthalten. Der gewünschte Effekt kann dadurch sogar ins Negative verkehrt werden.
Problem von Isolationsbohrungen im Metallträger
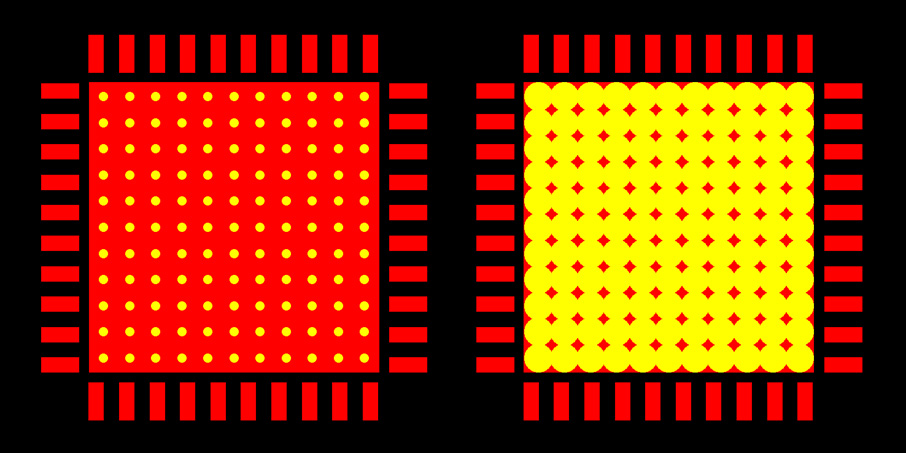
Eine Ausnahme oder Alternative bilden sogenannte Wärmefallen-Sacklöcher in Kupfer-IMS-Leiterplatten. Denn während man Aluminium nicht mit Durchkontaktierungen anbinden kann, ist dies mit Kupfer als Metallsubstrat möglich. Hier müssen keine größeren Isolationsbohrungen vorgebohrt werden.
seit dem Jahr 2021
- CO2-neutral durch Kompensation
- Leiterplatten - außen grün, innen auch
- Expertise durch aktiven Austausch
- Expertise durch Schulung und Weiterbildung

- ISO 9001:2015 Qualitätsmanagement
- ISO 14001:2015 Umweltmanagement
- UL für starre FR4-Leiterplatten
- UL für flexible Leiterplatten
- UL für ALU IMS Leiterplatten