SBU | PCB | HDI | Sequentieller Aufbau
SBU vs. HDI Leiterplatten
Oft werden HDI-Leiterplatten (High-Density Interconnect) und SBU-Technologie (Sequential Build-Up) in einem Atemzug genannt, als wären diese Technologien unmittelbar miteinander verbunden. Doch während SBU eine klar definierte Technologie bezüglich des erforderlichen Herstellungsprozesses beschreibt, sagt HDI nicht viel mehr als “es ist kompakt, fein und eng” auf der Leiterplatte. Technologisch verwoben sind diese beiden Technologien also daher, dass sehr kompakte Leiterplatten aus Platzgründen häufig feine Bohrungen erfordern, die sich nicht konventionell mit einem einzigen “DK-Bohr-Prozess” herstellen lassen.
Der Grund liegt in dem sogenannten Aspekt-Ratio, welches eingehalten werden muss, um gesicherte Durchkontaktierungen in Löchern herzustellen: werden Löcher sehr dünn, benötigen aber eine hohe Tiefe, stößt der Durchkontaktierungsprozess an Grenzen, da das Kupfer mit immer tieferen und engeren Löchern schwächer abgeschieden werden kann.
Die Lösung? Mehrfache Bohr-DK-Press-Prozesse, also ein sequentieller Aufbau → “SBU”, wie weiter unten erläutert.
Zusammenfassung:
HDI = Sehr feine Strukturen
SBU = Mehrfachverpressungen
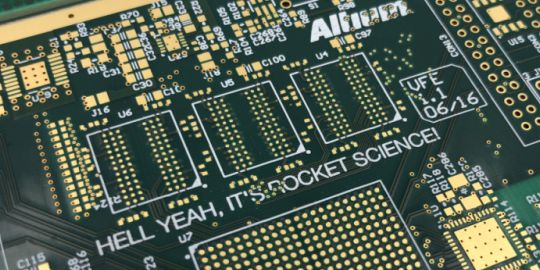
Die Grenzen, wann ein HDI-Aufbau als “High-Density” gilt, werden durch den technologischen Fortschritt stetig weiter verschoben. Galten vor wenigen Jahren noch Strukturbreiten von 100µm Leiterbahn/Abstand und 0,20mm Bohrungen als HDI, redet man heute ab 75µm Strukturbreiten mit 0,10mm Laser-Bohrungen in 0,30mm Pads von HDI.
Zurück zu der Frage: kann es das eine ohne das andere geben?
Nehmen wir einen einfachen 4-Lagen Multilayer, welcher extrem Kompakt designt wird und an die Grenzen des technisch machbaren bezüglich Bohrungen und Strukturbreiten geht: es handelt sich dann um einen HDI-Aufbau. Da ein 4-Lagen Multilayer aber maximal einen Pressvorgang haben kann, wird dieser definitiv nicht sequentiell aufgebaut. Es handelt sich also nicht um einen SBU.
Ähnlich sind andere Konstellationen als sehr dünne 6-Lagen Multilayer nur mit Blind-Vias denkbar, die keinen sequentiellen Aufbau (SBU) erfordern. SBU Leiterplatten sind aufwändiger herzustellen und prinzipiell dann notwendig, wenn konventionelle DK-Bohrungen, Buried Vias oder Blind Vias nicht viel Platz haben aber tief in den Multilayer vordringen müssen. Theoretisch sind sequentielle Aufbauten mit weiten Strukturen und breiten Bohrungen möglich, aber rein technologisch nicht nötig und unwirtschaftlich.
Fazit:
HDI ohne SBU → möglich und nicht unüblich
SBU ohne HDI → möglich, aber eher unüblich
SBU-Leiterplatten gelten meist als HDI!
Im Folgenden wird ein üblicher 6-Lagen SBU-Multilayer in seinen Prozessschritten erklärt. Zur Veranschaulichung der prinzipiellen Vorgehensweise sind Einzelprozesse teilweise miteinander zu einem einzigen SBU-Prozessschritt kombiniert.
Die später im Zentrum liegende Innenlage wird konventionell gebohrt und durchkontaktiert.

Es erfolgt die erste Verpressung mit Kupferfolie beidseitig, sodass ein 4L-Multilayerpaket entsteht.
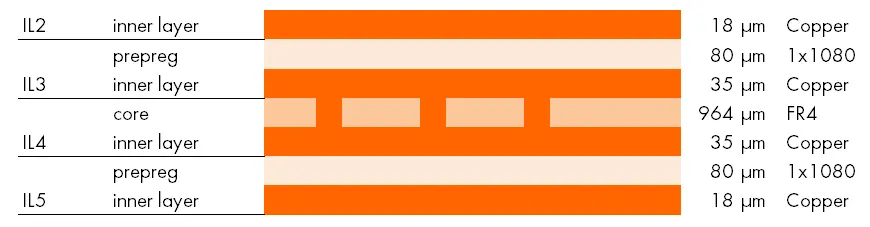
Das 4L-Paket wird mit zum zweiten und dritten Mal gebohrt, da die Sacklöcher von beiden Seiten erfolgen müssen, um darunterliegende Bohrungen zu treffen - es entstehen nach der zweiten Durchkontaktierung gestapelte VIAs. Die Leiterplatte wird anschließend zum zweiten Mal strukturiert.
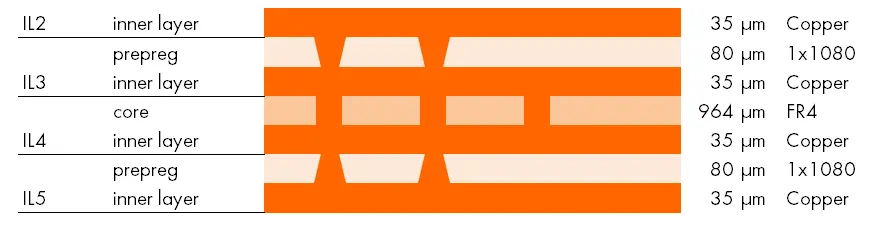
Zum zweiten Mal wir Kupferfolie beidseitig aufgepresst, um aus dem 4L-Multilayer ein 6L-Multilayerpaket zu fertigen.
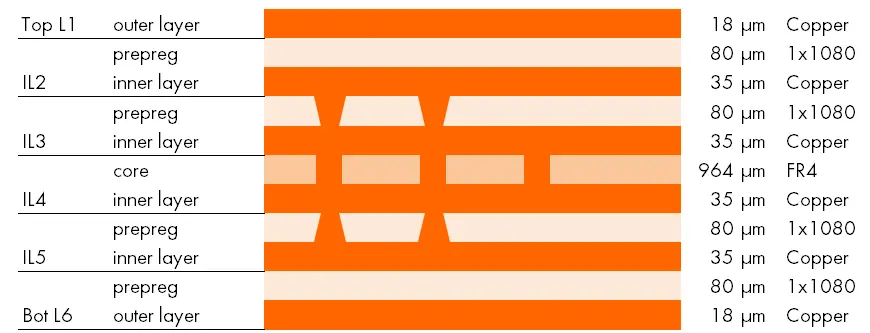
Das 6L-Multilayerpaket wird zum vierten und fünften Mal gebohrt - denn wieder werden beidseitig Sacklöcher hinzugefügt, die innenliegende Bohrungen treffen (es entstehen wieder gestapelte VIAs). Es können sie auch nur normale Durchkontaktierungen durch die vollständige Leiterplatte gebohrt werden. Es wird anschließend zum dritten Mal durchkontaktiert und zum dritten Mal strukturiert.
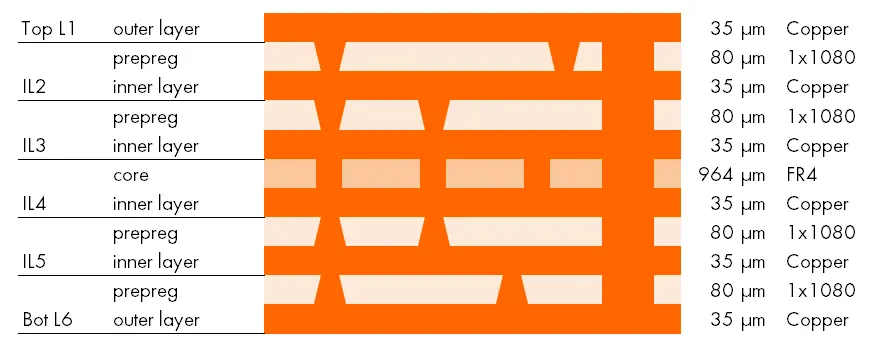
Abschließend wird der fertige 6L-SBU Multilayer oberflächenbeschichtet, mit Lötstopplack versehen, getestet und ausgefräst.
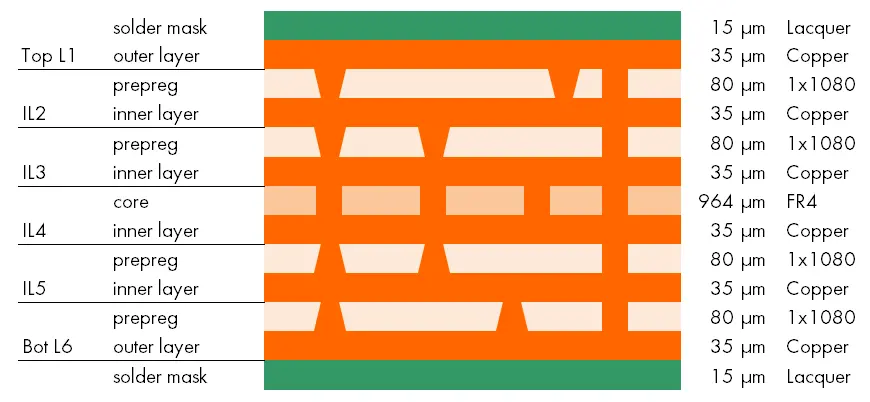
seit dem Jahr 2021
- CO2-neutral durch Kompensation
- Leiterplatten - außen grün, innen auch
- Expertise durch aktiven Austausch
- Expertise durch Schulung und Weiterbildung

- ISO 9001:2015 Qualitätsmanagement
- ISO 14001:2015 Umweltmanagement
- UL für starre FR4-Leiterplatten
- UL für flexible Leiterplatten
- UL für ALU IMS Leiterplatten