Climate neutral | PCB | environment |CO2 compensation
Climate-neutral circuit boards through compensation
Leiton becomes climate neutral - since 2021 we have been offsetting the CO2 emissions of all printed circuit boards we supply. This includes not only the electricity consumption, but also the CO2 emissions of the necessary raw materials such as copper, epoxy and fiberglass. Of course, transport should not be forgotten either. Here even the CO2 emissions of the deliveries from Asia and to you are compensated - whether by air, by train or by sea freight.
The environment is very important to all of us. So we decided to act. The manufacture of printed circuit boards not only requires a number of materials, it is also energy hungry. In addition, circuit boards are heavy and sometimes have long transport routes to get to you. All of this creates harmful CO2. It is not possible to directly prevent these CO2 emissions in printed circuit board production. Therefore, the CO2 emissions caused are determined in detail by Leiton and neutralized in the balance sheet through a compensation donation.
Another advantage for your own climate-neutral further processing is that you can use the Leiton circuit boards in your balance sheet with 0t CO2 emission, as we have already compensated for this.
The following factors, among others, are taken into account when determining CO2 emissions:
- Electricity consumption for the production of printed circuit boards in the respective production facilities
- Transport emissions from production facilities to us in Berlin - also from Asia
- Production of the base materials: epoxy, fiberglass, copper, aluminum, polyimide
- Transport route to you, the end customer
- Electricity and heating at the Berlin location
- Employee travels to work places
- All business travel
An expansion of the resulting CO2 emissions in other areas of the supply chain, as well as for disposal, are planned.
The numbers at a glance
Aufforstung über PRIMAKLIMA
The resulting CO2 emissions are offset in the balance sheet via PRIMAKLIMA (www.primaklima.org) by supporting reforestation projects.
PRIMAKLIMA is one of the most recognized organizations for offsetting CO2 emissions. Since 1991 PRIMAKLIMA has enabled reforestation- worldwide. The newspaper Finanztest gave the overall rating VERY GOOD (1.5) in the test 03/2018 PRIMAKLIMA
Test 03/2018 durch "Finanztest" - PRIMAKLIMA
Quality judgement: VERY GOOD (1,5)
Quality of compensation: VERY GOOD (1,5)
Transparenyc: VERGY GOOD (0,5)
Management and control: VERY GOOD (0,5)
You can find the complete test on "Stiftung Warentest"
The Kibale National Park in Ugandc
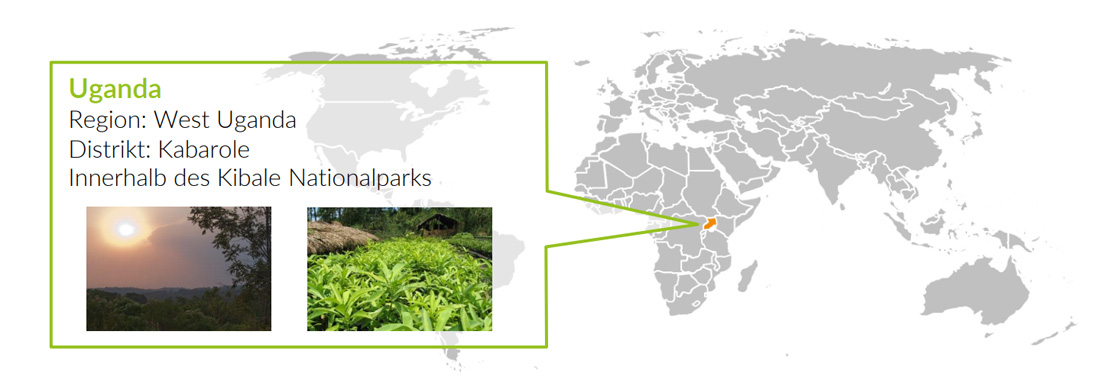
We are currently supporting a project to reforest rainforest areas in the Kibale National Park in Uganda. In addition to binding CO2, reforestation with native plants ensures a return of rainforest vegetation and the associated increase in biodiversity. The care and protection of the rainforest in the project area also provides various training and work opportunities in the forest sector, which offer important, alternative income opportunities. The implemented measures create further synergies, such as a growing number of providers of eco-tourism in the region, which in turn increases the acceptance of the protection of the rainforest and the income in the region over the long term.
In addition to the world's largest chimpanzee population, a dozen other primate species find protection in the Kibale National Park. African elephants, various wild cats and 370 counted bird species also live in the project area. An unbelievable 350 different tree species have been identified in the mixed forest.
Helfen Sie mit
You too can support environmental projects around the world with printed circuit boards from Leiton.
If you are interested in actively compensating for your CO2 emissions, contact us so we can share our experience and help you.
Because the climate concerns us all.
RoHS = Restriction of the use of certain Hazardous Substances. This law regulates the use of certain dangerous substances in electronics devices and printed circuit boards.
WEEE = Waste from Electrical and Electronic Equipment.This law regulates the recycling obligations for electronics and printed circuit boards.
Yes, RoHS/WEEE compliance is assured for all our products. You can download a RoHS-compliance test report in our download section.
One exception is the deliberate choice of leaded HAL surface finish. This surface finish is extremely seldom and is only offered on explicit enquiry. In this case we do explicitly explain that the product is not RoHS/WEEE compliant.
- Lead (as soldering surface finish "tin-lead")
- Halogenes (flame retardants)
- Bromides (PBB and PBDE)
A frequently requested declaration of RoHS/WEEE compliance can be found on the delivery note. Here we do declare RoHS/WEEE compliance for each delivered product.
In case you require a RoHS/WEEE compliance marking on the printed circuit board, please enquire. We can add such logos on request.
By mixing lead and tin at a 62:38 rate we reach an „eutectic point“. Here, the melting point is at around 183°C. Pure lead Blei has a melting point of 327°C and pure tin of 232°C. So a mixture is having advantages for saving energy and reducing stress of the printed circuit board and the components.
Due to lead-free soldering processes today, there are generally higher soldering temperatures required. This leads to additional stress for the PCBs and components and has made soldering rather more complicated. A lead-free soldering does not only include the printed circuit surface finish but also solder pastes and soldering tins.
Immersion tin RoHS-compliant
This is a chemical/physical process in which solute tin depostis on copper pads evenly. For two reflow soldering processes an immersion tin thickness of at least 1µm is required (1,2µm recommended).
Advantages of immersion tin | Disadvantages of immersion tin |
---|---|
Planare surface finish | Maximum storage time 6 months |
Good for fine-pitch applications | Not suitable for bonding |
Best surface finish for pressfit | Very sensitive, e.g. fingerprints can hinder soldering |
Widely accepted in Europe | Multiple reflow soldering steps not recommended |
Cheap | Tin thickness severly reduced after first soldering step |
HAL-lead free RoHS-compliant
In this process, hot tin is melted onto the PCB surface by diving the printed circuit into a tank of hot tin and blowing off residual tin with high air pressure directly afterwards (HAL = Hot Air Leveling). Usually, 15µm HAL-tin is on the centre of pads while edges have around 5µm.
Advantages HAL-lead free | Disadvantages HAL-lead free |
---|---|
Easy to solder thanks to large tin deposit on pads | Surface finish less planar than immersion surfaces |
Widely accepted in Europe | Not suitable for bonding |
Maximum storage time 12 months | Limited usability for fine-pitch due to uneven structure |
Notso senstive, e.g. to finger prints | Limited mutliple reflow soldering steps |
Cheap and fast process | High thermal stress during PCB production |
Immersion gold (ENIG) RoHS-compliant
ENIG stands for "Electroless Nickel Immersion Gold" and is a chemical/physical process in which first solute nickel deposits on the copper pads, followed by a thin layer of gold on top of that. Surface thicknesses according to IPC-4522 for nickel is 4-6µm and for gold 0,05-0,10µm.
Advantages immersion gold (ENIG) | Disadvantages immersion gold (ENIG) |
---|---|
Very good solderability | Very expensive process |
Perfect for fine-pitch applications | Requires intensive monitoring and expertise |
Maximum storage time 12 months | Requires highly poisonous chemicals |
Ultrasonic bonding with aluminium wire possible | Irreversible process |
No copper dilution into soldering bath because nickel acts as barrier | Very aggressive process (can attack solder mask) |
Very good for multiple soldering steps |
Immersion palladium-gold (ENEPIG) RoHS-compliant
ENEPIG stands for "Electroless Nickel Electroless Palladium Immersion Gold" and is a chemical/physical process in which first solute nickel deposits on the copper pads, followed by a thin layer of palladium and then gold on top of that. Surface thicknesses according to IPC-4556 for nickel is 4-6µm, palladium 0,1-0,2µm and for gold 0,02-0,05µm. This surface finish was newly developed to replace immersion thick-gold which used to have gold thicknesses of 0,3µm to 0,8µm in order to allow thermic gold wire bonding. Thanks to a substantially thinner gold layer this surface is gaining acceptance quickly.
Advantages immersion-palladium gold (ENEPIG) | Disadvantages immersion palladium-gold (ENEPIG) |
---|---|
Very good solderability | Very expensive process |
Perfect for fine-pitch applications | Requires intensive monitoring and expertise |
Maximum storage time 12 months | Requires highly poisonous chemicals |
Thermic bonding with gold wire possible, with some adjustments also ultrasonic bonding with aluminium wire | Irreversible process |
No copper dilution into soldering bath because nickel acts as barrier | Very aggressive process (can attack solder mask) |
Very good for multiple soldering steps |
Immersion silver RoHS-compliant
This is a chemical/physical process in which solute silver depostis on copper pads evenly. The deposited silver thickness is around 0,2µm.
Advantages immersion silver | Disadvantages immersion silver |
---|---|
Good solderability | Only offered by small selection of PCB suppliers |
Good for fine-pitch applications | Little acceptance in Europe |
Storage time 6 to 12 months | Sensitive surface finish due to very thin silver thickness. |
Cheap process | |
Widely accepted in the USA | |
Good for multiple soldering steps | |
Ultrasonic bonding possible |
OSP RoHS-compliant
OSP is a clear solder-lacquer. OSP stands for „Organic Surface Protection“ which explains that it is actually only meant to be a protection against corrosion of the copper. OSP is usually applied by spray-coating.
Advantages OSP | Disadvantages OSP |
---|---|
Planar surface finish | Bonding not possible |
Good for fine-pitch applications | Storage time only 3 to 6 months |
Used in low-cost mass production PCBs | Bad reputation due to negative market experiences with soldering lacquers in the beginning |
Very cheap and fast process | Offered by very few PCB suppliers |
Electrolytic gold / hard gold RoHS-compliant
A 4µm nickel surface is applied, followed by an electrolytic gold deposit. Due to solute cobalt this gold surface is much harder than usually. Gold thicknesses may range between 0,5µm and 1,2µm today, while in the past thicknesses of 3 to 6µm were common. Due to higher gold prices and little sustainability gains by such thick surfaces this is not available anymore. Electrolytic gold is commonly used for connectors and sliding contacts.
Advantages hard gold | Disadvantages hard gold |
---|---|
Perfect surface finish for connectors, sliding- and pressure contacts | Extremely expensive process due to high gold costs |
Storage time unlimited | Bonding not possible |
Very save and easy process | Difficult to solder |
Irreversible process | |
Very aggressive process (can attack solder mask) | |
Requires so called "bus connections" which connect the pads that need plating with the outside of the PCB. Usually only possible for outer areas of the PCB, not for the entire board. |
HAL-leaded X not RoHS-compliant
In this process, hot lead-tin is melted onto the PCB surface by diving the printed circuit into a tank of hot lead-tin and blowing off residual tin with high air pressure directly afterwards (HAL = Hot Air Leveling). Usually, 15µm lead-tin is on the centre of pads while edges have around 5µm.
Advantages HAL-leaded | Disadvantages HAL-leaded |
---|---|
Easy to solder thanks to large tin deposit on pads and low eutectic point (melting point) | Surface finish is not RoHS/WEEE-compliant and therefore banned in many applications! |
Low stress for PCB due to lower temperatures | Very few suppliers still offer this finish |
Storage time up to 12 months | Uneven surface |
Not senstive, e.g. to finger prints | Not suitable for bonding |
Not suitable for fine-pitch due to uneven surface | |
Multiple reflow soldering steps not recommended |
"RoHS-compliant" means that the PCBs are fabricated with either immersion gold, immersion palladium-gold, immersion tin or HAL-lead-free. Which of these surface finished is eventually selected by Leiton for your pritned circuits depends on the current order situation. This option is the cheapest because you leave the choice to us. You may chose an explicit surface finish for a surcharge.
In case you are not sure whether RoHS-compliant surfaces do meet your requirements we offer detailed information about all the surfaces on this website above. To begin with, all surface finishes offered under the label "RoHS compliant" in our online calculation are solderable but may differ in planarity, bonding capability, storage time and sensitivity.
REACH = Registration, Evaluation, Authorisation, CHemicals
REACH is a regulation of the European Union in order to protect human health and environment that may be affected by chemicals. This is a constantly expanded list of so called "cadidates" of substances that must be avoided in printed circuits.
Yes, REACH regulations are fulfilled by all products. You can find a reference REACH test report for rigid printed circuit boards and flexible printed circuits in our download section.
One exception is the deliberate choice of leaded HAL surface finish. This surface finish is extremely seldom and is only offered on explicit enquiry. In this case we do explicitly explain that the product is not RoHS/WEEE compliant, which also means it is not REACH compliant.
Conflict minerals are illegally mined minerals from certain countries where its revenues are used to fuel local conflicts. Currently, this includes Congo, and its neighbouring countries such as Ruanda, Uganda and Burundi. The minerals in question are gold, tin and coltan, which are all used in the electronics industry.
Yes, all minerals (mainly gold and tin) are sourced from certified and identified smelters which do not process any conflict minerals. You can download the latest CFSI-CMRT template in our download section.
since 2021
- CO2 neutral through compensation
- Circuit boards – green on the outside, also on the inside
- Expertise through active exchange
- Expertise through training and further education

- ISO 9001:2015 Quality Management
- ISO 14001:2015 Environmental Management
- UL for rigid FR4 PCBs
- UL for flexible circuit boards
- UL for aluminum IMS boards