Leiton GmbH | PCB | manufacturing | Germany | Berlin | custom | prototyping | production
Leiton GmbH - custom PCB manufacturing and prototyping Germany
The main facility in Germany produces prototypes, small series, and medium series - with a delivery time of 2 working days or more. Additionally, we supply many technologies and cost-effective series from Asia. The headquarters in Berlin processes your inquiries and orders, managing projects globally in a cost-optimized manner based on technology, delivery time, and price sensitivity. In addition to the most comprehensive online calculator in Germany, Leiton has numerous technical advisors who support you in the development and implementation of your projects. Data preparation (CAM) and any clarifications occur exclusively with our Berlin team. The quality assurance team in Germany ensures optimal service, high accessibility, and competence. Extensive testing and laboratory equipment are available for analysis and quality control support.
First sample inspection reports and additional services, such as detailed measurement reports (profiles, dimensions, resistances, inductances, impedances, etc.), are possible, as well as the creation of free layer builds and production recommendations. With our extensive experience, we are your ideal partner for transitioning prototypes into production. We advise you on available materials, process steps, or technology options. Whether you desire samples and pre-series from Germany and/or China, we are familiar with the differences and pitfalls, ensuring smooth transitions. Additionally, we offer cost-optimized transport options from Asia (sea-rail-air), affordable annual productions, and a large stock directly in Berlin.
- Printed Circuit Boards "Made in Germany"
- from 2 working days production time
- Technology Advisory Team in Berlin
- CAM processing in Germany
- laboratory and testing equipment
- Express prototypes to large series
- Wide selection of special technologies
- Comprehensive online calculator
Prototypes Made in Germany
Prototypes and express small series with a delivery time of 2 working days in the highest "Made in Germany" quality. In German manufacturing, only high-quality materials from Panasonic, NanYa, and TCLAD (Bergquist) are used. For multilayers, for example, a halogen-free mid-high-TG 150 from Panasonic is standard. In addition to an extensive and modern machinery park, it is especially the specialization in rigid printed circuit boards that guarantees consistent quality and high delivery reliability.
Due to the location in Germany, we are capable of delivering throughout the year, even during international holidays, such as the Chinese New Year. Prototypes are easily and conveniently calculable and orderable in our online calculation tool in many variations and with various additional and special technologies (blind vias, special prints, special colors, semi-flex deep milling, etc.).
- Manufacturing in Germany
- Prototypes and small series
- High-quality materials
- Delivery reliability through specialization
- Capable of delivering throughout the year
- Many special technologies
- Calculable online
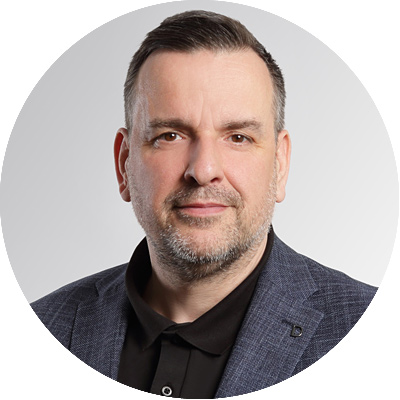
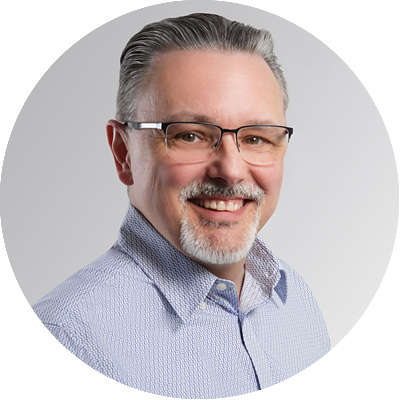
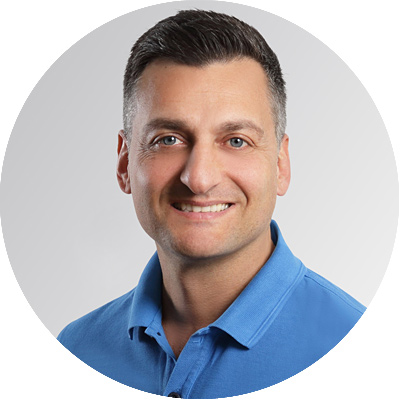
Service
Leiton embodies service, and therefore, we offer a variety of services beyond the actual circuit board. In addition to comprehensive online information, our technology experts in Berlin can be consulted at any time. The offering extends beyond data verification, technology recommendations, and material advice.
Individual measurement reports can be created, or various framework and call-off storage conditions can be agreed upon, significantly optimizing both quality and liquidity.
- Technical contact persons in Berlin
- Consultation on special technologies
- Data verification in Berlin
- Quality assurance teams in Germany and China
- Measurement reports & special requirements
- Stock retrieval and framework orders
- Double quality control
- Series transfer
- Online: Information, tools & downloads
since 2021
- CO2 neutral through compensation
- Circuit boards – green on the outside, also on the inside
- Expertise through active exchange
- Expertise through training and further education

- ISO 9001:2015 Quality Management
- ISO 14001:2015 Environmental Management
- UL for rigid FR4 PCBs
- UL for flexible circuit boards
- UL for aluminum IMS boards