Semi-Flex PCB | Flex-to-Install | Depth-Milling
Semi-Flex PCB Technology – Flexible Installation Without Connectors
With simple depth-milling a standard printed circuit board can be prepared for flexible installations. So called "semi-flexible" printed circuits are offering a cost-efficient solution. They save connectors and increase reliability while decreasing size of the application and time needed for assembly. Semi-flexible PCBs are the perfect solution if you have flex-to-install requirements only and there is no dynamic bending during operation.
Often layout designers are reluctant to upgrade from a standard PCB with connectors to a notoriously expensive rigid-flexible printed circuit. The advantages are immense, but so are the costs and the layout requirements compared to standard PCBs. Many times this "jump" from standard technology to a high-tech segment is not necessary. Many printed circuits do not require dynamic bending capabilities in operation but only need to be fit into the housing neatly. This is called a "flex-to-install" requirement and here semi-flex offers a really cost-saving alternative technology.
Production of a semi-flexible PCB is identical with the manufacturing process of standard printed circuits. Semi-flexilbe boards can be produced as single-layer, double-layer or multilayer PCBs. With the exemption of a special solder mask that sustains bending, the materials are also identical to standard printed circuits. The only difference happens at the end of the production process when dedicated bending areas are milled down by z-axis routing. The remaining material can be bend and is thin enough to only carry the copper traces and little base material.
To optimize transportation-safety and assembly, semi-flexible PCBs should always be produced in panels. You can easily seperate the prints from the panel after assembly and install the boards.
Design and installation of semi-flexible PCBs require some attention and modifications:
1. The PCB should only be bend with copper on the outside of the bending area.
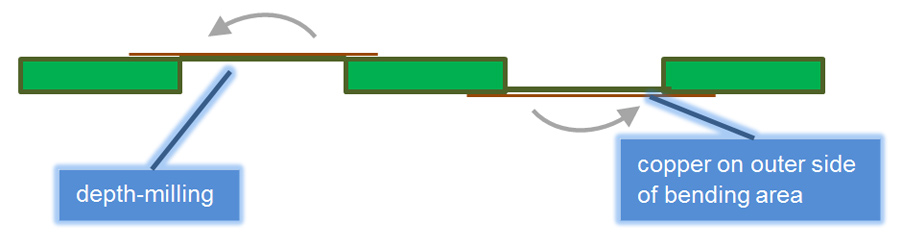
2. Open copper structures, pads, annular rings or vias in the rigid part of the PCB should have a distance of at least 1mm from the bending area. In special cases 0,8mm are okay, too. The semi-flexible are cannot contain any vias, drills or open copper structures. The transition area from flexible to rigid should have a radius of 5mm or an obstuse angle. Trace-to-outline distance in the semi-flexible area should be minimum 0,30mm.

3. The maximum bending radius depends on the lenght of the semi-flexible area:
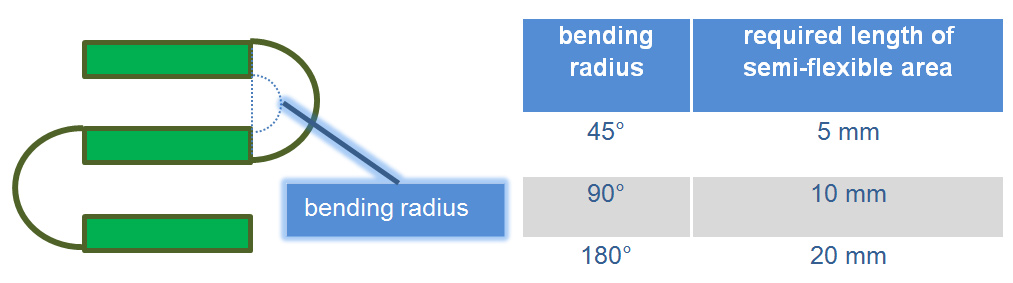
4. Currently, semi-flexible PCBs are possible up to 8 layers, while only one outer layer can be "semi-flexible" per bending area.
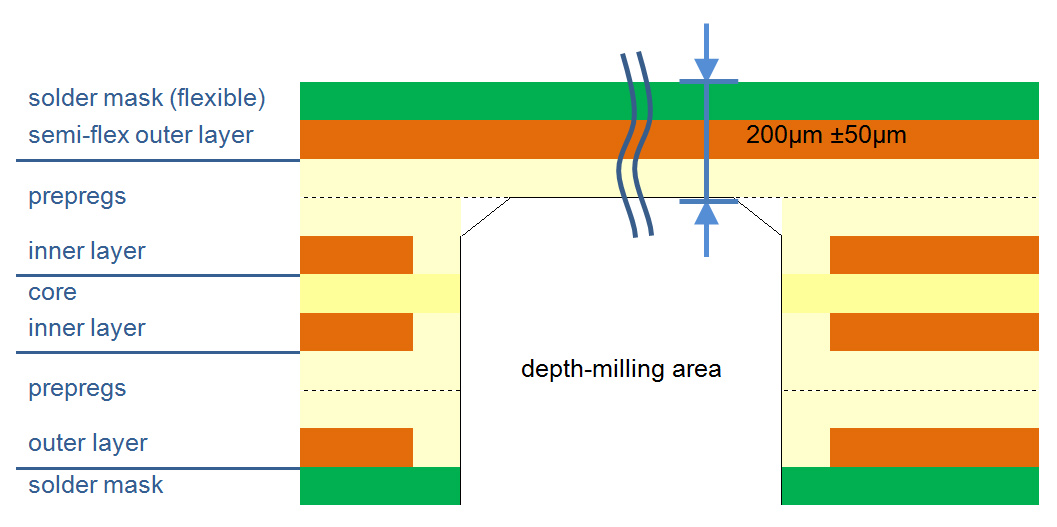
5. For the bending process we reommend to do this under hot air (you may use a hair dryer) and bend it over a fixed object in order to do so evenly.
Characteristic | Values, description |
---|---|
material type | FR4, Tg 130°C and some high-Tg materials up to 170°C |
remaining material | 150µm to 250µm |
maximum beding radius | 180°, depending on semi-flex area |
copper thickness | 35µm |
maximum layers | rigid area up to 10 layers, semi-flexible area one layer (outer) |
solder mask | flexible solder mask, green (for beding) |
bending | flex-to-install, not suitable for dynamic bending |
prints | partial silk print or other solder mask colours possible, not receommended in bending area |
depth-milling | digital z-axis milling, camera controlled, tolerance +/-20µm |
Your advantages of semi-flexible printed circuits compared to standard PCBs with connectors or rigid-flexible PCBs are the following:
- Semi-flex-PCBs are cheaper, because it is a "mainpulated" standard product that does not require connectors, nor expensive rigid-flexible PCBs.
- Semi-flex-PCBs are more reliable, because weak spots like connectors are avoided.
- Semi-flex-PCBs are easy to install, because bending it into place is much easyer than using additional connecting parts.
since 2021
- CO2 neutral through compensation
- Circuit boards – green on the outside, also on the inside
- Expertise through active exchange
- Expertise through training and further education

- ISO 9001:2015 Quality Management
- ISO 14001:2015 Environmental Management
- UL for rigid FR4 PCBs
- UL for flexible circuit boards
- UL for aluminum IMS boards